В эпоху цифровой трансформации производственные предприятия активно ищут пути оптимизации и автоматизации процессов оперативного учёта и управления. Многие компании сталкиваются с искушением развивать для этого старую или новую ERP-систему, игнорируя разницу между ERP и MES – специализированным решением для управления производством (Manufacturing Execution System).
На первый взгляд это кажется логичным – зачем внедрять дополнительную систему, если уже есть мощный инструмент, охватывающий большинство бизнес-процессов? Однако сравнение ERP и MES доказывает, что такой подход приводит к снижению эффективности, потере реального контроля за производством и упущенным возможностям.
Попытка «натянуть» функционал и решение задач оперативного управления производством на ERP – это все равно что пытаться использовать грузовик для гонок «Формулы-1»: он может двигаться, но никогда не достигнет нужных скорости, маневренности и точности. Тем не менее, к сожалению, таких «грузовиков», которые пытаются ехать по гоночным трассам российских производств, довольно много. Более того, удивительно, что до сих пор есть примеры и попытки создания функционала MES внутри существующих ERP-систем от известных вендоров.
Основные отличия ERP и MES: разные задачи – разные инструменты
MES – это «центральная нервная система» предприятия. Если ERP – «мозг» компании, управляющий финансами и ресурсами, SCADA – «руки», непосредственно взаимодействующие с оборудованием, то MES – это «спинной мозг», который соединяет стратегическое планирование с тактической реализацией. Различия между ERP и MES становятся очевидны при анализе их функций:
- ERP оперирует агрегированными данными (недели, месяцы), отвечая на вопросы «Что?», «Когда?», «Сколько?».
- MES работает в реальном времени, управляя конкретными процессами: «Что происходит на станке сейчас?», «Какое сырьё используется?».
Согласно стандарту ISA-95 для каждого уровня управления требуется специализированное решение. Отличия ERP и MES здесь фундаментальны: первая – для стратегического планирования, вторая – для оперативного контроля.
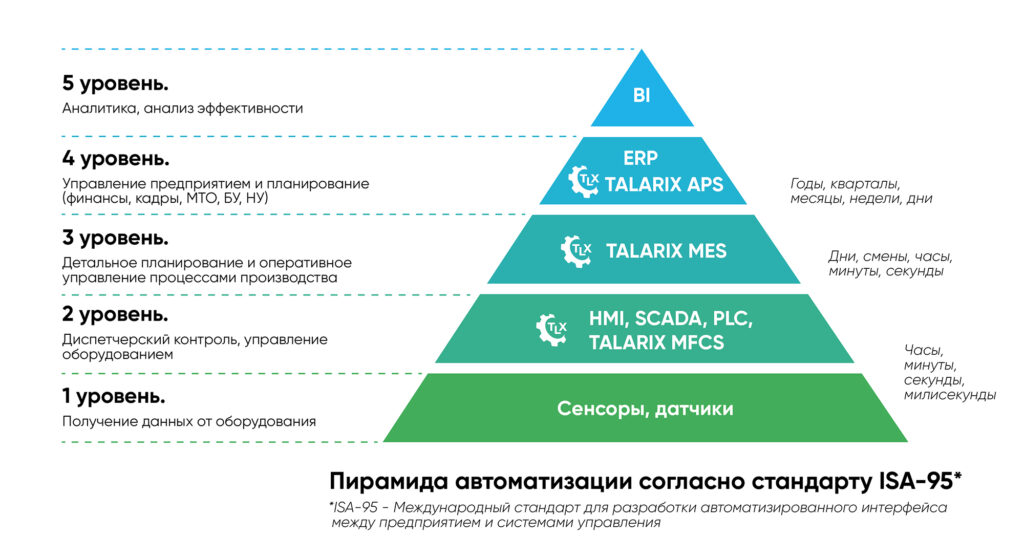
Соответственно, ERP оперирует агрегированными данными, часто с временным горизонтом в недели, месяцы или даже годы, а MES живет в совершенно ином измерении – в реальном времени, или близком к нему, и здесь важны не агрегированные показатели за месяц, а то, что будет происходить на конкретном станке, с конкретной партией сырья, с конкретным оператором прямо здесь и сейчас или в ближайшую производственную смену.
Задачи, которые обычно стремятся решить производственные предприятия
На практике производственные предприятия, которые занимаются поиском решения для повышения эффективности, прозрачности, оперативного управления, цифровизации в целом, интересуются темой промышленного интернета вещей (IIoT), планируют решить и автоматизировать у себя на предприятии следующие задачи:
- оперативное производственное планирование, ресурсное и пооперационное;
- диспетчеризация (мониторинг и управление) производственных процессов;
- оперативный учёт операций на производстве;
- полная сквозная прослеживаемость сырья и материалов;
- управление и контроль качества (QM);
- планирование и управление ресурсами (люди, оборудование);
- интеграция с производственным оборудованием (конвейеры, принтеры, весы, сканеры и т.д.);
- предоставление актуальных данных (запасы сырья по партиям в разрезе складов, процент выполнения производственных заданий, процент выполнения отгрузок и т.д.).
Почему же ERP-системы неэффективны в решении этих задач?
Разберём более детально фундаментальные, в том числе архитектурные, различия между MES и ERP с точки зрения их применимости для решения бизнес-задач.
Основные недостатки ERP
- Несоответствие временных масштабов. ERP-системы спроектированы для работы с дневными, недельными и месячными периодами, в то время как управление производством требует реакции в масштабе секунд и минут.
- Отсутствие специализированных производственных функций. ERP-системы не предназначены для детального оперативного отслеживания производственных параметров и данных по объектам производственного учёта, анализа простоев и эффективности оборудования (OEE – Overall Equipment Effectiveness), управления качеством в режиме реального времени.
- Архитектурные ограничения. Архитектура ERP оптимизирована для обработки транзакционных бизнес-процессов, а не потоков производственных данных большого объема. Попытка построить MES-систему на архитектуре и процессах, реализованных в ERP, как правило, приводит к сложным и неэффективным решениям, с низкой производительностью, ограниченной функциональностью и высокой стоимостью поддержки уникальными специалистами, знающими конкретное решение в данных условиях.
- Сложность интеграции с оборудованием. ERP-системы, как правило, не имеют встроенных механизмов для прямого подключения к SCADA, PLC и другим промышленным системам управления.
- Избыточная нагрузка на сеть и сервера. Попытка обрабатывать производственные данные в ERP приводит к перегрузке инфраструктуры и снижению производительности всей системы.
- Критическая инфраструктура. Производственное оборудование, автоматизированные системы, в том числе MES, на большинстве предприятий относятся к критической инфраструктуре, от доступности и стабильности функционирования которых зависят работа всего предприятия, его показатели и результаты. Поэтому и требования к уровню доступности MES-систем на некоторых предприятиях доходят до 99%. С MES внутри ERP этого обеспечить невозможно как минимум потому, что ERP требует довольно частых обновлений с учётом изменения законодательства и обновлений, связанных с реализацией изменений под требования бизнеса. Подобного показателя можно добиться только с использованием отдельной MES-системы, которая настроена под процессы конкретного предприятия, в которой исключены или минимизированы влияния на её работу со стороны смежных блоков (закупок, продаж, логистики, финансов и др.).
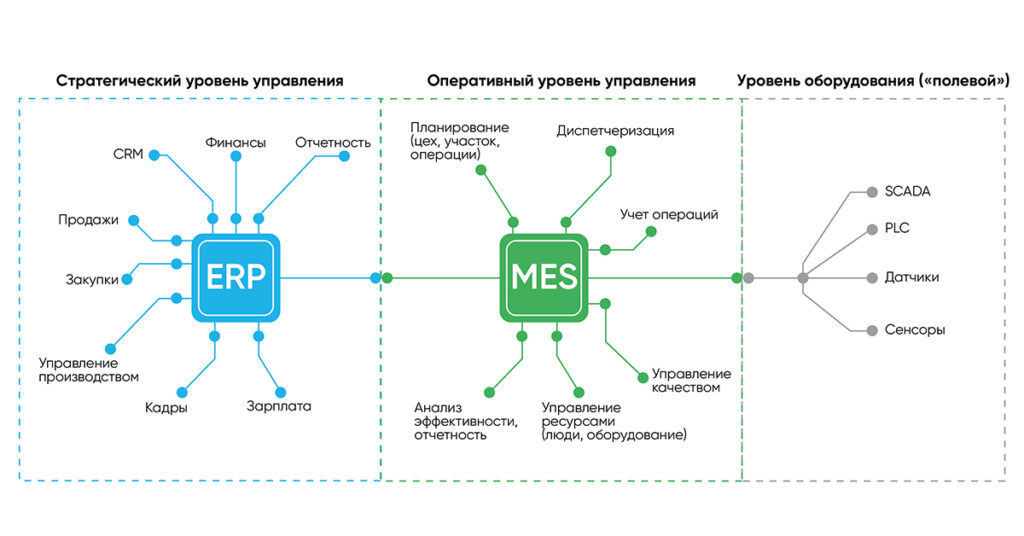
Преимущества специализированных MES в отличие от ERP
- Управление в режиме реального времени. MES-системы спроектированы для оперативной реакции на события в производстве, что критически важно для современных предприятий.
- Оптимизация производственных процессов. MES позволяет детально анализировать и оптимизировать технологические процессы, сокращать время переналадки, минимизировать простои как оборудования, так и работников на участках.
- Повышение качества продукции. MES включает функции контроля качества на всех этапах производства, что снижает процент брака и повышает лояльность клиентов.
- Прослеживаемость производства. Доступна полная история изготовления каждого изделия, включая используемые материалы, параметры оборудования и действия персонала.
- Сбор и анализ больших объемов производственных данных. MES спроектированы для эффективной работы с большими потоками данных, получаемых с производственного оборудования. Тем не менее нужно также принимать во внимание, что для получения данных в режиме реального времени используются промежуточные системы (Data Logger), позволяющие собирать данные с OPC серверов оборудования.
- Специализированные интерфейсы для рабочих мест. Интерфейсы MES разработаны для удобного и эффективного использования на производственных участках с учетом специфики рабочих процессов.
- Четкое разделение ответственности. ERP управляет бизнес-процессами на уровне всего предприятия, MES – процессами и задачами на уровне производства. Каждая система делает то, что умеет лучше всего.
- Обмен данными. Совмещение всей возможной функциональности и процессов в единой системе из-за представления, что обмен данными – это ненадёжно, сложно и неправильно, – стереотип, которому давно не место в современном мире и подходе к построению архитектуры ИТ-систем.Актуальный подход предполагает создание композитной архитектуры с созданием интеграционного ландшафта через сервисную шину данных (Enterprise Service Bus, ESB). Она обеспечивает гарантированный и прозрачный обмен данными и предоставляет единую точку интеграции для всех систем предприятия, включая ERP, MES, PLM, LIMS и других.
- Скорость обработки информации. Для ERP скорость обработки информации, например, при планировании или проведении документов, не так критична. Скорость обмена данными с оборудованием, ввода и обработки информации на производстве напрямую влияет на его производительность и эффективность. Поэтому архитектура современных MES-систем изначально проектируется с учётом требований к работе в режиме реального времени, обработки большого массива данных, удобства работы и интеграции с оборудованием и другими системами.
- Гибкость и масштабируемость. При необходимости можно модернизировать или заменить любую из систем без серьезного влияния на другие компоненты архитектуры и производство. Например, модификации ERP не влияют на работу MES и не требуют остановки производства для тестирования, обновлений, откатов из-за возможных ошибок.
- Повышение надежности. Распределенная архитектура с четким разделением функций повышает общую надежность и отказоустойчивость ИТ-инфраструктуры.
Если обращаться к истории крупнейших вендоров, в частности такой компании, как SAP SE, стоявшей у истоков создания ERP, то SAP изначально не стал развивать функциональность MES как часть ERP и уже в начале 2000-х годов выпустил отдельную систему SAP ME (SAP Manufacturing Execution), которая интегрирована с ERP через шину данных.
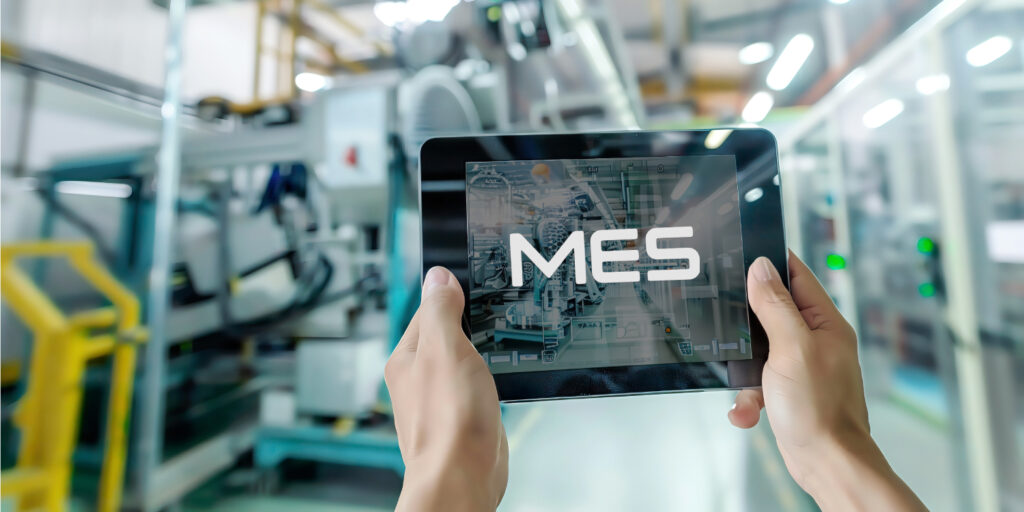
Учитывая очевидные идеологические и архитектурные различия в системах ERP и MES, а также международные стандарты и опыт, на сегодняшний день вендоры и заказчики должны понимать эти различия как при разработке, так и при выборе системы для автоматизации производственных процессов своего предприятия.
Реальные эффекты на производствах
Поскольку MES-системы для многих современных производственных предприятий уже давно являются неотделимой от производственного процесса сущностью, накоплено довольно много аналитики и статистики как западных, так и российских компаний по реальным эффектам для бизнеса от использования MES.
При этом нужно принимать во внимание, что эффекты от внедрения MES могут варьироваться и зависеть от отрасли, масштаба компании, исходного состояния производства, качества проекта внедрения, сопутствующих технологических и организационных изменений, которые дают комплексный эффект.
Ниже приведены средние показатели эффектов в разрезе отраслей из открытых аналитических источников.
Машиностроение и металлообработка
- Сокращение цикла производства: 20-35%
- Повышение OEE: 15-25%
- Увеличение выработки: 10-20%
Источник: CESMII – The Smart Manufacturing Institute
Нефтехимия и фармацевтика
- Сокращение брака: 20-45%
- Повышение соответствия нормативным требованиям: 30-60%
- Сокращение времени выпуска партии: 15-30%
Источник: ISA-95 Industry Group Analysis
Пищевая промышленность
- Снижение производственных потерь: 12-24%
- Повышение эффективности использования сырья: 8-15%
- Сокращение энергопотребления: 10-22%
Источник: Food Processing Suppliers Association
Заключение
Современное производство требует специализированных инструментов для каждого уровня управления. В отличие от ERP, MES-системы, разработанные в соответствии с международными стандартами и взаимодействующие с ИТ-ландшафтом предприятия в режиме реального времени, обеспечивают оптимальное сочетание управленческого контроля и производственной эффективности.
Инвестиции в отдельную MES окупаются за счет снижения издержек, повышения производительности, улучшения качества продукции и обеспечения соответствия нормативным требованиям.
В эпоху «Индустрии 4.0», цифровой трансформации, промышленного интернета вещей MES-система – это не просто конкурентное преимущество, а необходимое условие выживания и развития предприятия, дающее как краткосрочные, так и долгосрочные эффекты.